Product Description
AGV intelligent Porter (car)
Intelligent Porter / logistics handling robot AGV
AGV (Automated Guided Vehicles) aka AGV automatic guided vehicle, car, laser navigation.Its remarkable characteristic is unmanned, AGV equipped with automatic guiding system, can guarantee the system without needing to manually pilot cases can along the predetermined route automatic travel, goods or materials automatically from the starting point to destination.AGV is another feature of good flexibility, high degree of automation and high intelligent level, AGV route according to the storage space requirements, production process of change and flexible change, and running path change costs traditionally associated with the conveyor belt and the rigidity of the transmission line is very low.AGV generally equipped with loading and unloading mechanism, and other logistics equipment automatic interface, realize the goods and material handling and transportation of whole process automation.In addition, AGV also has a clean production characteristics, AGV relies on its own battery to provide power, during the operation of no noise, no pollution, can be used in many of the requirements of clean working environment.
A AGV category
AGV from the invention has 50 years of history, with the expansion of application fields, the types and forms of diversified.According to AGV automatically in the running process of navigation of the AGV is divided into the following types:
1 electromagnetic induction guided AGV
Electromagnetic induction type guide is usually on the ground, along the predetermined route laying wires, when high frequency current flows through the wire, the wire electromagnetic field generated around, AGV are arranged symmetrically two electromagnetic sensors, they received electromagnetic signal intensity differences can reflect the degree of deviation from the path of AGV.AGV automatic control system according to the deviation to control the steering of the vehicle, a continuous dynamic closed loop control can ensure AGV to set the path stability automatic tracking.The electromagnetic induction guided navigation method is present in the vast majority of commercial AGVS use, especially suitable for large and medium-sized AGV.
2 laser guided AGV
The AGV are rotatably mounted on the laser scanner, the running path along which the walls and pillars are installed on the high light reflection plate laser positioning mark, AGV relies on a laser scanner emits a laser beam, and then accepted by the surrounding landmarks is reflected back into the laser beam, the on-board computer to calculate the vehicle current position and movement direction, through and the built-in digital map compared to the correction range, thereby realizing the automatic handling.
At present, the AGV application more and more widespread.And according to the same guiding principle, if the laser scanner for infrared transmitter, or replacement of an ultrasonic transmitter, then the laser guided AGV into infrared guided AGV and ultrasound guided AGV.
3 visual guide type AGV
Visually guided AGV is undergoing rapid development and maturation of the AGV, the AGV CCD is installed on the camera and sensor, in the computer is provided with AGV to route the surrounding environment image database.AGV during the running process, dynamic camera for vehicle surroundings image information and image database are compared, so as to determine the current position and the next step driving decision making.
The AGV due to not ask for help to set any physical path, so in theory has the best guide flexible, with the computer image acquisition, storage and processing of the rapid development of technology, the utility of AGV is more and more strong.
In addition, there are magnetic gyro inertial guidance type AGV, type AGV optical guide and other forms of AGV.
Two AGV applications
The 1 storage industry
The storage industry is the first of AGV applications.In 1954 the world's first AGV in the United States of America South Carolina Mercury Motor, Freight company warehouse operation, for the realization of the automatic handling of goods storage.The world has about 20000 various AGV run in 2100 greatly small warehouse.Haier Group in 2000 and put into operation the Development Zone warehouse, 9 AGV composed of a flexible storehouse automatic handling system, successfully completed every 23400 out of storage of goods and components handling task.
2 manufacturing industry
AGV in manufacturing production line display one's skill to the full, efficient, accurate, flexible material handling task.And can be composed of multiple AGV consisting of a flexible logistics transportation system, transportation route with the production process of adjustment and adjust in time, make a production line capable of producing more than 10 kinds of products, greatly increasing production flexibility and competitiveness of enterprise.In 1974 Sweden Volvo Kalmar car assembly plant in order to improve the transportation system flexibility, based on AGVS for vehicle automatic car assembly line, the assembly line is composed of multiple loading car body AGVS components, the assembly line, assembly time is reduced by 20%, reduce 39% assembly failure, investment recovery time is reduced by 57%, labor is reduced by 5%.At present, AGV in the world's major automobile plant, such as general, Toyota, Chrysler, Volkswagen and other auto factory manufacturing and assembly line to obtain the widespread application.
In recent years, as the basis of CIMS handling tool, AGV is used in processing machinery, household appliances manufacturing, microelectronics manufacturing, tobacco and other industries, production and processing field to become the most widely used fields AGV.
3 post office, library, port and Airport
In a post office, library, port and airport and other occasions, the delivery of existing operation volume changes, dynamic, operation process is often adjusted, as well as handling operation process of single features, AGV parallel operation, automation, intelligent and flexible characteristics can be very good to meet on occasion handling requirements.Sweden in 1983 in Stockholm, Japan Post Office on 1988 in Tokyo Tama post office, China in 1990 to Shanghai postal center began to use AGV, finished products handling work.In Holland Rotterdam port, 50 units called "yard tractors" AGV containers from the ship transported to a few hundred yards outside the warehouse of the repetitive work.
4 tobacco, pharmaceutical, food, chemical industry
For handling a clean, safe, no pollution and other special requirements of the tobacco, pharmaceutical, food, chemical industry, the application of AGV had also been seriously.In many domestic cigarette enterprises, such as Qingdao Etsong group, Hongta group, Yuxi Honghe Cigarette Factory, Huaiyin cigarette factory, the application of laser guided AGV complete pallet cargo handling.
5 dangerous places and special industry
In the military, with AGV autopilot based on integrated with other detection and removing device, can be used for battlefield reconnaissance and ground clearance, the British military was developed by MINDER Recce is a reconnaissance vehicles, with mine detection, destruction and route verify the ability of the automatic reconnaissance vehicle.In the iron and steel factory, AGV for charge transport, reduces the labor intensity of workers.In nuclear power plants and the use of nuclear radiation preservation storage sites, AGV used for goods transportation, avoids the risk of radiation.In the photographic film and film warehouse, AGV can be in the dark environment, accurate and reliable delivery of materials and semi-finished products.
SMT special AGV
The version of AGV used for handling PCB frame, and transported to the designated on the board or plate above, achieve the empty PCB frame recovery or a full frame handling, in order to fit the space is compact, line spacing is narrow, common AGV can not achieve a good turn and, plate butt.He developed a PCB frame handling for AGV, the AGV has a forward, backward, turn left and right, bifurcation function, and has a transverse movement function, and docking equipment using 2 positioning, ensures that the 5mm positioning accuracy, and the realization of the equipment the perfect combination.
Operation circuit diagram
SMT special AGV specifications
Dimensions of L960*W520*H1050 (mm)
Walking mode for magnetic guidance
The walking direction of forward and backward, turn around, bifurcation, lateral movement
Wireless local area network communication function (optional)
Drive 4 drive
Driver DC24V
Carrying capacity of 150Kg (or custom)
Ontology model SMT special type
Walking speed 30-40m/ velocity (or custom)
Minimum turning radius of up to 300mm (tape line laying radius)
The navigation accuracy of ± 10mm
Work 24 hours
Gradeability up to 3-5 degrees
Stop accuracy of ± 10mm
Charging mode manual charging (optional automatic charging)
Safety induction range ≤ 3M, adjustable, emergency braking distance is less than 20mm
Alarm mode acousto-optic alarm
Battery maintenance-free rechargeable batteries, continuous discharge number >300
Safety protective obstacle detection sensor + mechanical anticollision mechanism of double protection
Design life of >10 years
Dedicated SMT AGV architecture
Payment Terms︰
RMB
Lead Time︰
20D
Product Image
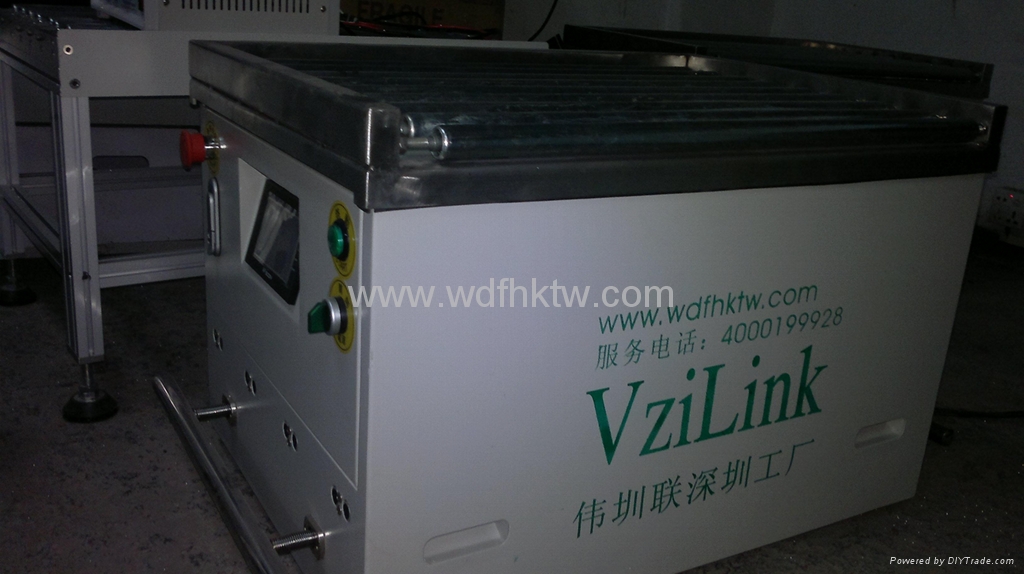
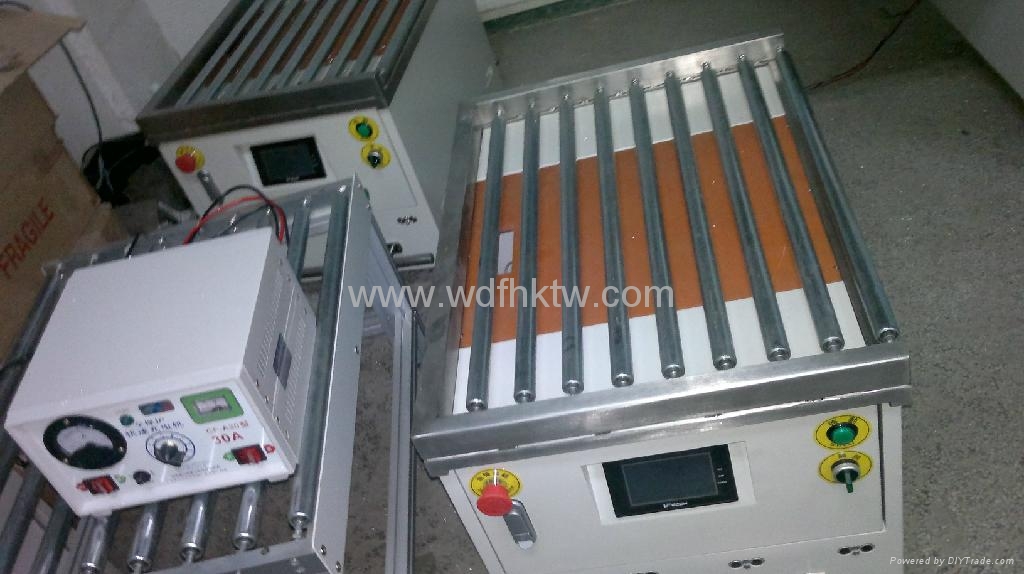
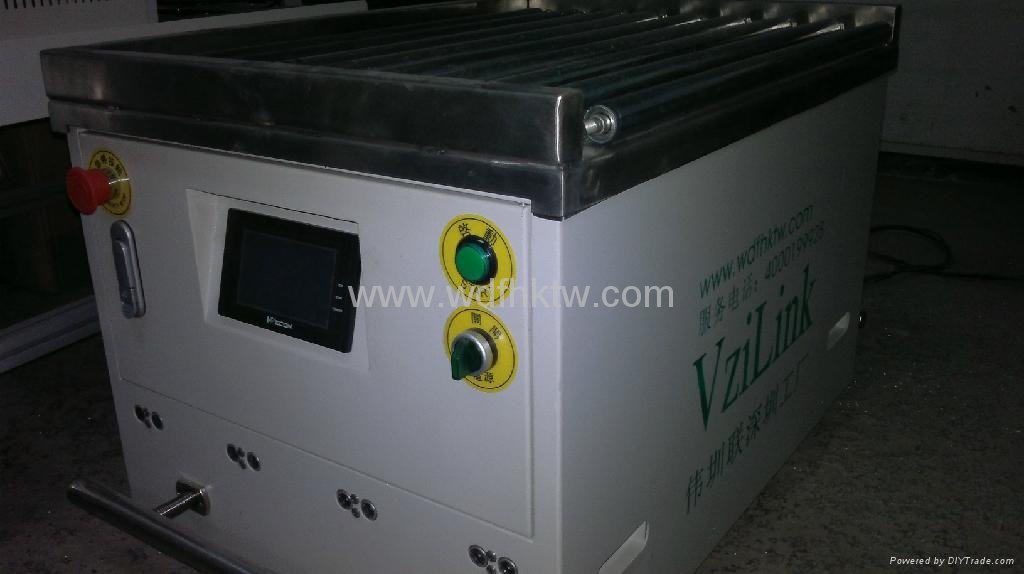
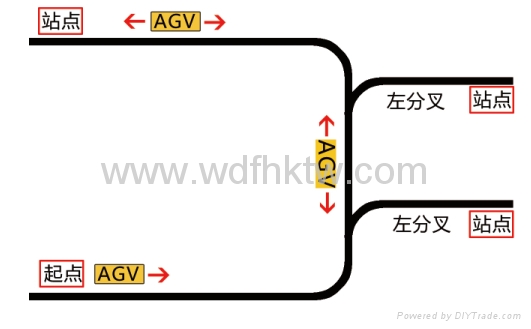
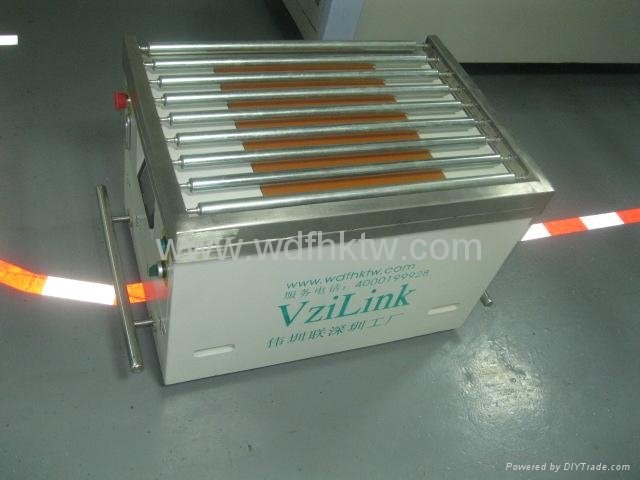